摘 要:基于传统量热仪技术升级换代要求,利用严格水套密封包围工艺结构设计了新型绝热式智能量热仪系统。采用ARM嵌入式技术开发了量热仪的定制触摸屏操作系统,利用ARM微处理器开发了系统的主控制器,采用具有高增益、高分辨率、低漂移特性的数模转换器,设计了量热仪的四路温度数据采集调理电路,采用分段式PID控制原理设计了量热仪的内、外筒水温自动跟踪控制算法,并对系统进行了测试实验。
关键词:量热仪; 绝热式;分段PID;嵌入式系统; 温度采集
我国是产煤大国,而衡量煤炭质量的最重要指标之一是其燃烧发热量。目前国内普遍采用以发热量作为动力煤计价的主要依据[1]。由于煤炭的发热量主要是利用量热仪来测定,其测量精度和效率直接影响着煤炭企业的经济效益,同时也在节能减排、环境保护等方面发挥着极其重要的作用。
传统的煤发热量分析方法是利用氧弹热量计进行人工测定,操作繁琐、费时费力[2],并且容易产生偶然误差和计算错误。鉴于此,本文采用ARM嵌入式系统开发了一种新型绝热式智能量热仪,该系统以ARM微处理器为主控制单元,采用严格水套密封包围工艺结构,选用高精度的铂电阻PT1000为温度传感器;采用新型A/D芯片组成四路高增益、高分辨率、低漂移特性的温度数据采集调理电路,利用分段PID控制原理设计智能量热仪的外、内筒水温自动跟踪控制算法;采用触摸屏技术实时动态地显示内外筒水温。测试结果表明,该绝热式智能量热仪的性能指标满足设计要求。
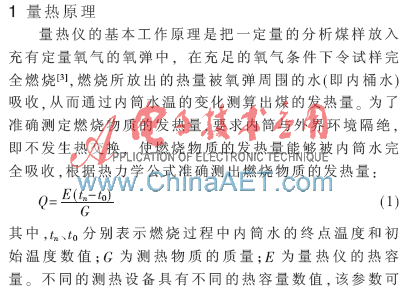
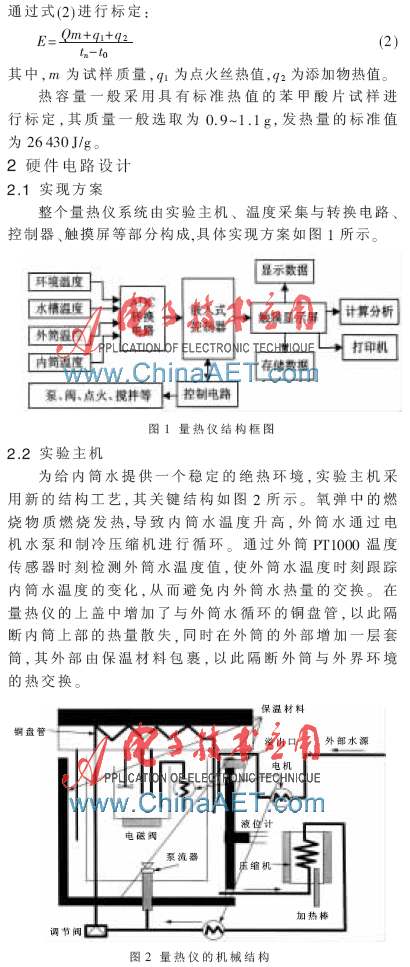
2.3 ADC转换电路
考虑本系统输入信号的变化非常灵敏,微机控制单元接收和处理PT1000热电偶感测的温度数据采集速度较慢,及极低噪声的要求,本文采用一种新型高精度24位ADC转换芯片CS5534设计智能量热仪的4路温度数据采集ADC转换器电路。
CS5534芯片是美国Cirrus Logic公司推出的一种具有极低噪音的多通道Δ-Σ型A/D转换器,该芯片采用电荷平衡技术和极低噪声的可编程增益斩波稳定测量放大器,得到高达24位分辨率的输出结果,精度高,动态特性宽。可编程增益放大器可使放大倍数从1~32进行设定(以2倍步长增加), 大大提高了系统的动态特性。该A/D转换器还有一个灵活而简便的同步串行接口,使转换数据以串行方式输出,并与SPI、Microwire兼容[4],串行时钟输入备有一个施密特触发器。采用串行接口与中央处理器芯片通信工作,接口电路设计简单、易于扩展。
2.4 ARM控制器
控制器主要控制4路PT1000温度传感器采集内外筒水温度数据,检测、显示量热仪的工作状态,控制量热仪的自动进水和出水,控制外筒水温度实时跟踪内筒水温度的变化,精确控制压缩机制冷和加热棒加热动作,实时控制量热仪的工作状态,检测燃烧物质的燃烧状态,控制搅拌电机工作等功能,并且能够与触摸屏及A/D装置进行实时数据通信,显示通信状态,与打印机实时通信完成试验结果的打印。
本文控制器采用具有ARM核的STM32F103单片机作为主控芯片。该芯片是一款基于CortexTM-M3核心的32 bit低功耗MCU[5],工作电压为2.0~3.6 V,主频达72 MHz,1.25 DMIPS/MHz。具有睡眠、停机和待机3种省电模式。内括12 bit的ADC、DMA控制器;支持定时器、ADC、DAC、SPI、I2C、UART等外设;提供欠压复位、ECC、MPU、侵入监测、双看门狗、32 bit CRC、I/O端口保护和JTAG熔断器等安全功能。综合各项参数,STM32是最适合本系统的微处理器之一。
2.5 触摸屏
触摸屏的作用是通过触摸点检测装置接收触摸信息,并将其转换成触点坐标送给CPU,同时接收、执行CPU发来的命令。本系统采用威纶通公司的MT8000触摸屏,它与控制器采用Modbus协议进行数据通信。触摸屏系统采用组态软件设计,具有实时数据显示与存储、历史数据查询、故障报警等功能,并能将内外筒水温度状态进行动画显示。
3 软件设计
3.1温度控制算法设计
温度控制系统是一个大惯性、大滞后系统,绝热式智能量热仪的关键问题是:煤样在燃烧过程中发出的热量导致内筒水温度急剧升高。为杜绝内筒水热量与外筒间的热传导,需要实现外筒水温度实时跟踪内筒水温度的变化。鉴于此,在本系统中设计了分段PID控制算法,PID参数可随温区的不同自动调整到最佳值。整个测温范围分为平衡阶段和升温阶段,在平衡阶段仅仅接通外筒水槽中的小加热棒,PID控制算法驱动该加热棒与制冷压缩机工作状态平衡,其平衡温度点由系统工作需要设定;在煤样燃烧启动接通大加热棒时, 通过PID控制算法参数的调节作用控制外筒水温度, 并迅速跟踪内筒水温度的变化,从而消除内外筒之间水的热交换,保证内筒中PT1000热电偶测得的水温全部由煤样燃烧引起。
3.2 STM32与A/D的数据传送控制设计
本系统需要完成四路PT1000温度传感器的数据采集与传送控制,STM32需要实现对A/D数据采集通道的选择、初始化操作、功能与时钟设置、A/D通道的读写操作、采集数据计算等。本设计采用STM32操作系统中的SPI函数来实现,具体程序代码略。
3.3 STM32与MT8000触摸屏的通信设计
MT8000触摸屏采用Modbus协议和控制器单元进行数据通信。Modbus通信协议只能识别按地址发送的消息,这就要求得知每个控制器的设备地址,才能执行相应的控制动作。如果需要回应,则控制器将生成反馈信息并用Modbus协议发出,具体程序从略。
3.4 STM32的串口通信设计
STM32控制芯片支持UART串口通信、I2C通信和SPI串行通信协议,本系统采用RS-323进行串口通信,具体程序从略。
4 试验
仪器试验具体操作过程为:
(1)水槽加水,仪器上电,加热棒或者压缩机自动工作调整水槽的水温度值,使水温和环境温度平衡(此时内筒底部的阀门处于关闭状态),外筒和水槽是连通的。
(2)当水槽、外筒水温和环境温度达到一致时,打开内筒底部的阀门开始进水,当水位升至内筒壁水位计时,阀门自动关闭,内筒水和外筒水环境断开。此时为了满足外筒水温高于内筒水温1~1.5 ℃的国标要求,加热棒开始加热工作,并检测内外筒水温是否达到一致,若达到,则停止加热。
(3)仪器开始搅拌5 min使内筒水温度分布均匀,期间外筒水在加热棒和压缩机的共同作用下始终沿着内筒水温度改变。
(4)搅拌5 min结束时,氧弹仓中煤样点火,内筒水温度急剧上升,同时检测到内筒水温度上升信号,水槽中的1 000 W加热棒开始加热。通过外筒与水槽的水循环,该信号立刻被外筒水温度传感探头检测到,外筒水温度开始跟踪内筒水温度急剧上升,其跟踪曲线如图3所示。
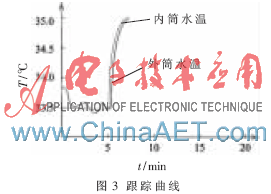
由图3可以看出,开始时外筒水温度向内筒水温度平衡,达到两者温度一致时,搅拌5 min使内筒水温度分布充分均匀,氧弹试样点火后内筒水温度开始上升,几乎同时外筒水温度开始跟踪内筒水温度变化,且两者之间的跟踪误差最大不超过0.5 ℃。对于绝热式仪器设计来说,0.5 ℃温度差导致的热交换基本可以忽略,因此,绝热式量热仪能够很好地消除内外筒之间的热交换问题。内筒水温度不再变化时,外筒水温度基本以小于0.1 ℃的超调量围绕内筒水温度变化,直至试验结束。实验测试数据如表1所示。
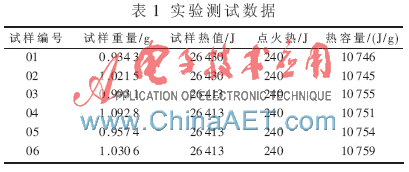
本文开发了一种高精度的新型绝热式智能量热仪系统,该系统采用了水套密封包围工艺结构、ARM嵌入式和触摸屏技术;采用了外筒水加热跟踪内筒水温度变化的控制模式,通过引入分段式PID控制算法提高了发热量测试结果的准确性和控制精度。试验结果表明,该仪器性能稳定、重复性好、准确度高,且操作方便,符合市场需求。
参考文献
[1] 李平, 姬建伟, 宋家友. C8051F350在恒温式自动量热仪设计中的应用[J]. 传感器与微系统, 2007, 26(10):
111-113.
[2] 刘辉,马凌云,何东陆. 一种煤炭自动量热仪的设计[J].工矿自动化, 2007(6):97-99.
[3] 陈宪. 恒温式自动量热仪使用的若干问题分析[J].华北电力技术, 2001(3):38-40.
[4] 申仲涛. 基于CS5534的成组接地线电阻测试系统[J]. 微计算机信息, 2009,25(6-2):288-290.
[5] 罗超,景林,易金聪.基于STM32的便携式海量温湿度记录仪设计[J]. 电子技术应用, 2012,38(12):83-86.