1 引 言
LED是一种绿色照明光源,其主要优点是发光效率高。随着材料科学的进展,在未来十几年其发光效率会有更大幅度的提高;且能量消耗低、寿命长、材料可回收,不会污染环境。
基于LED照明的以上优点,欧美、日本和韩国都制定了相应的法律法规和产业扶持政策,在未来十几年的时间里大规模推广相关技术到民用照明领域。我国虽然起步比较晚,但最近几年也开始了积极的科研开发和产业政策的制定和扶持等工作。
2 大功率白光LED路灯发光板设计的相关应用技术
目前,白光LED 技术主要有三种:采用InGaN蓝色LED管芯上加少量钇铝石榴石为主的荧光粉,由蓝光LED激发荧光粉发出黄光,与蓝光混合发出白光;利用三基色原理将红、绿、蓝三种LED混合成白光;用紫外光LED 激发三基色荧光粉产生多色光混合成白光。
其中第二种方案控制难度较高、而且阵列应用很难保证发出均匀的白光,而第三种白光技术所发白光有紫外光成分,因此这里选择第一种白光技术进行应用技术分析。大功率白光LED的发明成功为半导体发光元件进入照明领域提供了物质与技术保障。大功率白光发光二极管在照明领域的使用需要注意两方面问题:电/ 光转化率和发光组件的热控制。
大功率LED是一种小型器件,随着制造技术的提高,输入的驱动电流越来越大,输入功率也随之提高。虽然电/光转化率较高,但从芯片面积上来讲,应该算作是点光源,因此单位面积上发热量很大。而大功率LED器件性能随着结温的升高会受到很大影响,超过一定温度后,电/光转化率会急剧下降,甚至器件因为温度过高而永久失去功能。
2. 1 提高大功率LED 芯片电/光转化率并使芯片热流密度均匀化的芯片级应用技术
随着技术发展, LED的芯片二维尺寸不断地增大,通过扩大LED芯片面积,使得LED输出功率提高,发光亮度得以大幅度地提高。但若一味加大芯片面积,反而会出现LED 內部的光吸收比率增加、外部量子效率降低等不利的现象,并且结温的温升也会进一步升高。而且随着芯片二维尺寸的增加,芯片本身的发光效率也下降得很快。
为了优化LED芯片的热学、光学性能,一方面除了加大芯片的尺寸,另一方面可以通过优化芯片上电极结构使得整个芯片在工作时的电流均匀地扩散分布。如果电流分布不均匀,往往会导致热流密度以及光通量的不均匀分布,在芯片内部产生局部的热斑,这样将大大地降低LED器件的效率和可靠性。
为减少LED芯片中横向电流不均匀分布,有效电流路径长度必须很短并且同等,该长度决定于正电极和负电极的空间距离。图1(b)芯片电极通过优化后电流密度在整个芯片分布的均匀性要比图1 ( a)好。
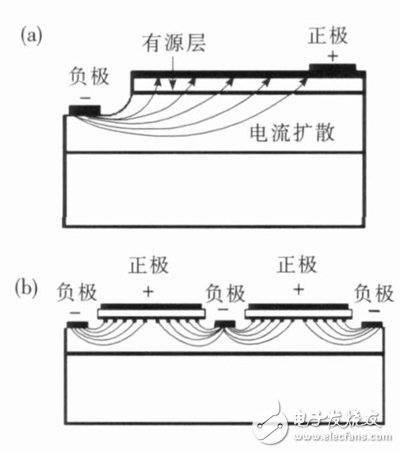
图1 LED中不同电极结构的电流扩展分布
可知对于大芯片LED,单独一个电极设计是不利于电流扩散,因此现在的大功率LED多采用梳状条形交叉电极、梳状条形与点状结合的电极以及米字形的电极结构设计。这可以使得芯片内电流分布比较均匀,使发光芯片由单电极结构的点光源成为面光源,提高芯片总的光输出通量,另外可以使得芯片的表面热分布均匀,防止产生热斑。图2所示为主流的大功率LED的电极结构示意图,其中的米字型电极设计的芯片为美国Cree公司的专利产品。
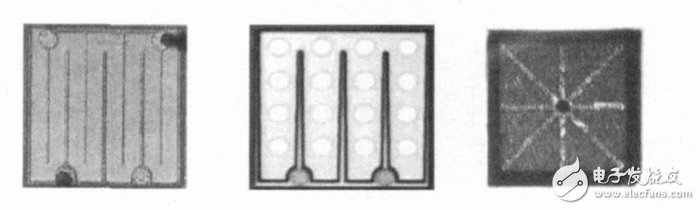
图2 大功率LED芯片电极结构。
米字形电极结构主要应用是基于导电碳化硅( SiC)衬底生长的LED,其电流是垂直扩散,比起在绝缘透明蓝宝石(sapphire)衬底上生长GaN基梳状电极的LED芯片的横向扩散电流,其电流分布均匀性更好。
2. 2 大功率白光LED 的封装阶段对LED 芯片取光、保障白光质量与器件快速散热技术的综合应用
固晶阶段:将LED芯片焊接固定在导热衬底(热沉)上,一般在衬底上由下而上地敷有绝缘层、电路层、反射层。图3~5为三种芯片在衬底上的焊接固定方式。
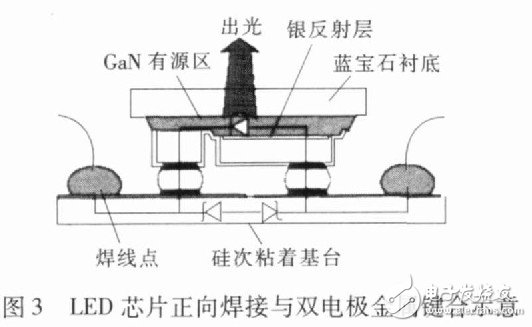
图3 LED芯片正向焊接与双电极金属键合示意
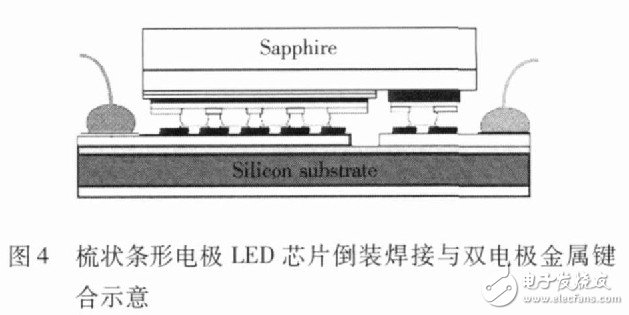
图4 梳状条形电极LED芯片倒装焊接与双电极金属键合示意
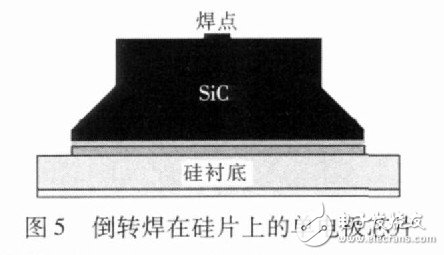
图5 倒转焊在硅片上的单电极芯片
其中图4 和图5 的固晶方式与图3 的常规LED芯片的固晶方式相比较,将芯片的发热端与热沉层直接接触,非常容易散热,将比较大的发光面朝上,既考虑了取光率也考虑了散热,这是目前主流的大功率LED芯片焊接固定方式。
安装管壳:安装的管壳一般都会被加工成锥形或抛物线形的反射杯,以增加功率型LED的出光量,属于二次取光技术, 增加了单芯片的出光率。
金属键合:利用金丝球焊的方法将焊盘与外部电极连接键合,即芯片电极与外部电极相连接。
配粉及涂粉工艺:配置可在蓝光LED发出的蓝光激发下能发出相应色谱范围内黄光的荧光粉,并涂敷在芯片的表面。涂敷荧光配胶工艺目前国内多采用传统的点胶方式,国外多采用保形涂敷( conformal coating)技术。二者比较而言,通过点胶形成的荧光粉层不能保证在芯片周围的厚度一致,这样就会造成不同视角发光器件的颜色不一样。而采用保形涂粉的方法,由于在芯片周围涂层的厚度均匀,因此所发出的光的颜色一致性好,保证了所发出白光的纯正。
最后,向反光杯( reffeitor)中填充热稳定性能好、绝缘以及光学透明折射率高的柔性硅胶,并在最上面加上一个光学透镜,形成光学微腔,经热固化后完成整个器件的封装。图6~8为单芯片封装的功率型的LED器件。在完成大功率白光LED芯片及封装的出光率与热管理的技术优化基础上,可采用COB技术阵列式组装大功率白光LED芯片制造路灯发光板。
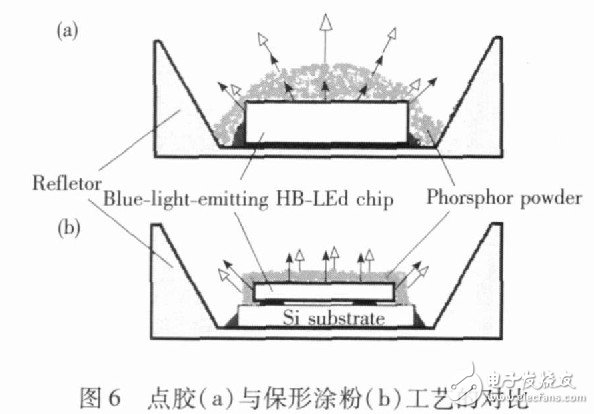
图6 点胶(a)与保形涂粉(b)工艺的对比
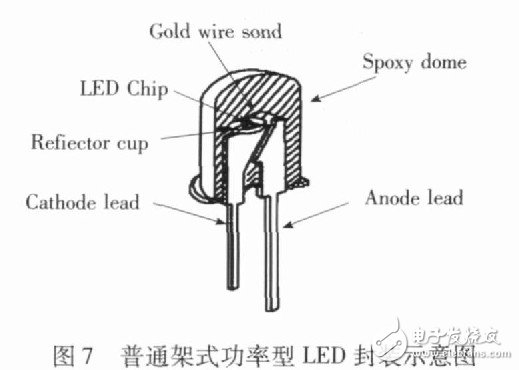
图7 普通架式功率型LED封装示意图
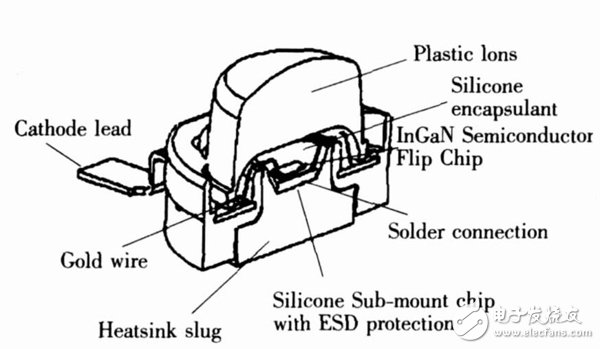
图8一种大功率LED器件的封装示意图
2. 3 以COB技术阵列式组装大功率白光LED路灯发光板的技术优势
LED产业经过40多年的发展,经过了支架式LED (Lead LED ) 、普通贴片式LED ( Chip SMDLED) 、功率LED ( Power LED) 、大功率LED (HighPower LED)等发展历程。
图9为LED发光器件封装结构的演变,从图中可以看出,LED器件封装的热阻越来越小。但是在目前的路灯应用上,相对而言大功率LED的光通量( lm)仍然有限,单管亮度还远远不够,必须配置多个LED器件组成阵列。
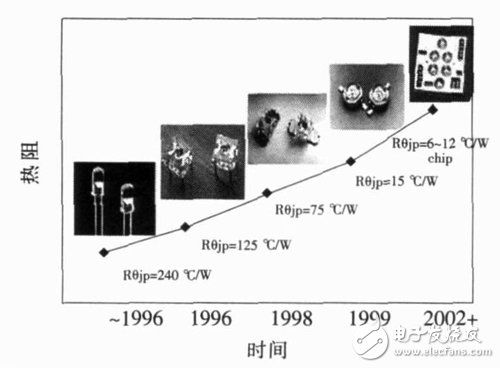
图9 LED封装结构的演变以及热阻的变化趋势。
对于架式功率型LED,因为单管光通量不足,只能集合多个LED元件组成LED阵列,分布焊接在PCB板上形成路灯用的发光板,以达到较高的光通量才能符合照明市场的需求。但是这种LED器件整个发光芯片是被聚脂塑料包裹,而聚脂塑料是一种热的不良导体,所以其自身发出的热量很难散失,因此也会很严重地制约功率型LED的发光效率。此外PCB 板也是热的不良导体,从LED下部也很难散热。
对于目前比较广泛使用的普通贴片式LED、功率LED器件虽然单管光通量有所提高,但是单管光通量还是不能符合照明市场的需求,要制成实用的照明灯具,尤其是路灯照明,采取的技术方案与支架式LED相同,将发光器件阵列式焊接在PCB板上形成较大光通量的发光板。但是每个功率型的单管LED下部都有高导热的热沉层,散热情况要好于架式的功率型LED.
但是这两个方案有一个共同问题,由于器件数量比较多,使电路的设计比较复杂,而电路板自身的基板由热的不良导体制成,灯具热流散发不畅,很难与各种外部散热手段(无论是主动散热,比如加装风扇式散热器等,还是被动散热,比如加装散热片等)兼容,影响了灯具的稳定性和使用寿命,故障率相对较高。
为解决以上问题,可以采用COB技术对LED芯进行阵列式封装,形成大的发光板。该组装方式在形成光学微腔的封装过程与单管大功率LED封装方式完全相同,只是以阵列的方式将LED芯片固晶在一块较大面积的敷有氧化膜绝缘层和电路层的高导热复合材料基板上。如图10和图11所示,典型的高导热复合材料衬底有美国Bergquist公司的T2Clad产品,德国Curamik覆铜陶瓷板DBC(Direct Bonded Copper)。使用成本更低廉的覆铜铝基板也可以达到同样的热沉效果(铝基板的氧化膜可承受1 000 V的静电击穿电压)。
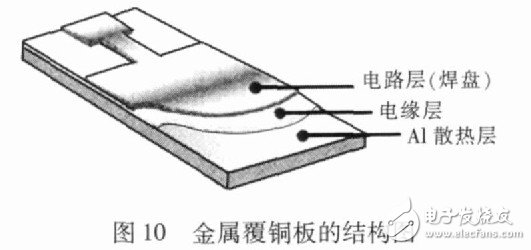
图10 金属覆铜板的结构图
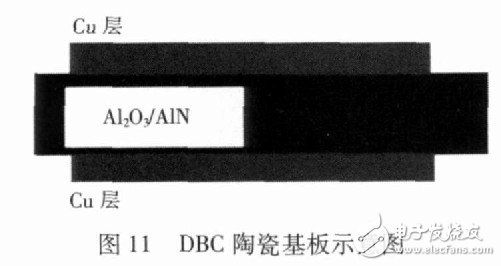
图11 DBC陶瓷基板示意图
相对于前两种技术方案来讲,采用COB技术将大功率LED芯片阵列式封装在复合材料线路板上有以下几点好处:
从散热管理的角度来讲,虽然贴片式LED(Chip SMD LED) 、功率LED (Power LED)器件在芯片下装有高导热材料的热沉层,但是从LED芯片依次向下有反射层、电路层、绝缘层、导热材料组成的热沉层,而各层之间粘合或多或少要使用一些不良的散热材料,此外,目前常规方案中使用的电路板的基板也是热的不良导体,因此对散热也很不利。而高导热复合材料是用共晶冲压的方式制造的,电路层、绝缘层、导热层之间结合紧密属于原子级结合方式,因此其散热率更是高于单管热沉层的散热率。
另外根据有限元分析软件对功率型LED组件热阻模型分析结果表明:对于采用高导热热沉的单管大功率LED的封装方案,外加散热基板面积的尺寸很大程度影响芯片的结温,在空气自然对流下,其直径要大于20 mm才能使得LED芯片在120 ℃以下工作。而采用的COB 技术封装的LED模块,很容易实现将LED 芯片工作结温控制在120 ℃以下。
实际上, COB封装技术和高热导率复合材料的结合,其优势更加体现在多芯片封装上,如图12所示,形成多芯片模块组件,有利于提高LED单位封装组件的散热性能,同时增加单位组件的发光亮度。而且高导热复合材料是电路与热沉的合成体,结构紧凑,在散热的同时也解决了电气连接的电路问题,并且由于电路层单面分布,可实现电热性能分开,与外部制冷器能很好的兼容,外部制冷组件可以直接贴在板后,进一步降低工作温度保证LED光源的可靠性和稳定性。另外,采用COB封装的制作工艺兼容于目前电路板制作流程,技术成熟可靠,可实现大规模量产。
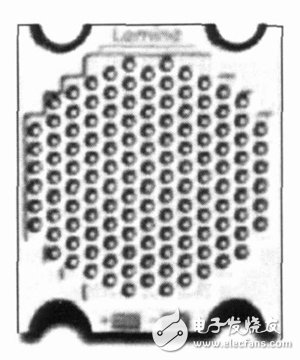
图12陶瓷基板LED阵列
采用半导体新型COB技术封装后,LED芯片直接封装在基板的铜线路层上,不用象单个功率型LED器件那样另外加工芯片热沉、电极引线框架以及塑料外壳等,能简化LED封装工艺,缩短封装流程,节约成本。
2. 4 以光线最佳归一化为标准计算COB组装的大功率白光LED 芯片阵列的芯片间距离
采用COB技术阵列式封装大功率白光LED芯片制造路灯照明发光板时,芯片间的距离对阵列的出光效率和热管理的影响也是一个很关键的因素。因为芯片工作过程中会不可避免的发热,如果靠得过近,整个面板的中间的高热区就会因为温升过快而影响灯具的正常使用,一般有可能会发生偏色,更严重的后果可能就是由于温度过高,散热不畅而导致LED发光器件失灵,造成整个发光阵列的开路,影响灯具的使用寿命和稳定性能。所以要避免这种不利的热管理状态。但是,如果距离太远,则可能会使出光后由于各点LED光源射出后在被照场内交叉覆盖不足即光线归一化不好而导致照明光强不均匀。
现在忽略芯片、封装材料以及空气三者之间界面的反射、折射以及全反射等光学现象。假设单芯片LED 光源为受限朗伯光源且为点光源,可表示为:

如果m = 1,那么LED光源就为完美的朗伯光源,考虑到实际情况,对于LED光源, m 》 1.而且m依赖与半角度θ 1 /2 (由制造商给出,定义为光照度下降到零度角光照度的1 /2 时的角度) ,一般可由式(2)表示:

根据平方反比定律可知,在直角坐标系中,在某一点P ( x, y, z)的光照度可以表示为式(3) :
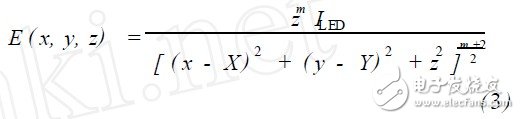
其中ILED =LLED ·ALED为LED的发光强度, LLED为LED芯片的亮度,单位cd /m2 ·sr, ALED为芯片的面积。
考虑只有两个LED的组成简单阵列情况,芯片之间的距离为d,那么两个LED组成的阵列的光照度公式(4)为:

通过调节两个芯片之间的距离d, 得到比较均匀的照明区域所示,通过对E求两次导,使得在( x,y) = ( 0, 0)的位置d2 E /dx2 = 0,得到最大平坦条件:
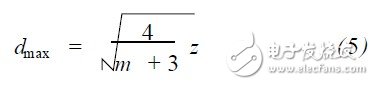
对于N ×N 阵列的LED模块:
当N 为奇数时,总的光照度公式(6)为:

当N 为偶数时,总的光照度公式(7)为:

计算各LED芯片间的距离的方法与两管的计算方法相同。图13为仿真模拟结果。当两个点光源的距离为dmax时在坐标零点附近的照度是均匀的,否则将出现暗区。
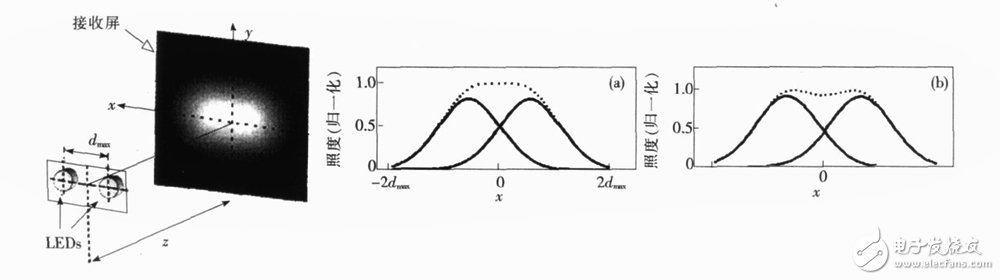
图13LED双芯片之间发光图样重叠(归一化)分布示意图( ( a) d = dmax , ( b) d 》 dmax )
3 大功率白光LED芯片阵列---路灯发光板的驱动与亮度调节技术
发光半导体属于直流驱动元件,驱动方式有:
恒压驱动有文献也称为电阻限流驱动方式和恒流驱动方式两种。相比之下,恒流驱动PWM调亮方式来驱动大功率白光发光二极管要优于恒电压驱动调节工作电流方式来调节亮度的方式。
因为大功率白光发光二极管只有在特定的电流区间内才能发出纯正的白光,对照明场景内的景物有最强的再现能力即演色性,但是这个电流范围非常窄。 LED 的响应时间一般只有几纳秒至几十纳秒,适合于频繁开关以及高频运作的场合,因此可以方便地通过周期性的改变脉冲宽度,亦即控制占空比的方式来实现对LED 亮度的调节,例如要将亮度减半,只需在50%的占空周期内提供电流就可以实现了。可选择200~300 Hz的开关频率来进行PWM亮度调节,这是因为人眼无法分辨超过40 Hz的频率的变化, 但是太高的频率又会引起白光颜色发生移位和亮度调节非线性, 恒流驱动PWM亮度调节方式是工作在某个特定的正向电流下, LED能显示出最纯的白光,不会象调节工作电流方式调节亮度那样随着工作电流偏离这个值,大功率高亮度白光LED发出的光会产生偏色现象。另外,大功率高亮度白光LED都是工作在大电流下,因此其在工作时必然会产生大量的热量。随着工作温度的升高,LED器件的性能会降低,因此散热对LED器件工作性能影响很大。在使用PWM控制方式时和脉冲平均电流和直流电流大小相等的情况时,LED器件会有更低的温度,外量子率比较高,所以有更高的发光亮度,也更加节电。而且PWM方式使用控制电路实现起来也比较容易。
4 结 论
在LED路灯发光板设计过程中要保证大功率白光LED的发光效率和每个LED芯片光发射的适当交叉覆盖。大功率白光LED 的发光效率与芯片设计、封装方式、驱动方式、温度等因素密切相关。为尽量提高大功率白光LED路灯发光板的电/光转化效率,设计中从大功率白光LED发光芯片设计入手,采用增加发光芯片面积、电极优化、发光芯片倒装焊接在高导热热沉材料衬底、保型涂粉等技术,保证了大功率白光二极管最大电/光转化率和所发出白光的均匀度。大功率白光LED毕竟属于点光源,发光过程中热量集中,并且当LED结温超过120 ℃时将产生严重光衰和偏色。根据有限元分析软件对单管大功率白光LED倒装焊接封装于高导热热沉层封装模型的热阻分析可知: 采用高导热热沉的单管大功率LED的封装方案,外加散热基板面积的尺寸很大程度影响芯片的结温,在空气自然对流下,其直径要大于20 mm才能使LED芯片在120 ℃以下工作。而采用的COB 技术封装的LED 模块,很容易实现在空气自然对流下将芯片工作结温控制在120 ℃以下,并可与外部散热技术良好兼容。在使用PWM控制方式时,当其脉冲平均电流和直流电流大小相等时, LED器件会有更低的温度,外量子率比较高,所以有更高的发光亮度,也更加节电,而且控制电路实现容易。
根据本文对大功率白光LED各项技术性能的分析,以及对LED阵列光线归一化数学模型的分析计算,设计试制了COB技术封装的大功率白光LED路灯发光板和采用PWM驱动控制的太阳能LED路灯控制器。
实际驱动的实验数据完全接近LED热阻模型有限元分析的结果。在空气自然对流状态下很容易控制在120 ℃以下,与普通PCB板大功率白光LED 阵列发光板相比较,散热温度至少低15℃,在实际控制中温度补偿最高上限在85 ℃( ±5 ℃)即可。经过连续半年的运行和实验测试,与同样光强的高压钠灯路灯相比,节能超过60%、光线归一化均匀柔和、未发现光衰现象。对大功率白光LED 路灯发光板设计具有指导意义。