上周俊知反馈一个高频机重大问题,发给两个客户的10来台机器,工作一会儿后就坏了,影响很坏,俊知负责人严厉质问,我因为没有负责生产,不了解情况,把问题转给了生产那边,那边给出的答案竟然是这一批的风扇质量有问题,18V工作电压下,电流竟然接近1A,而以前只有100mA附近。导致控制风扇的三极管烧坏继而引起跟风扇并联的继电器无法吸合而导致高频机无法工作。
再进一步问下去,他们生产前就发现了这个问题,提出了这个风扇不能用,但因为当时风扇缺,他们就把这个事情忘了,继续用了,而这个电流下,一二十分钟还测不出问题来,所以就发货了。
事情到这儿才刚开始,风扇与一个控制整个系统电源的继电器是同一三极管控制的。也就是说风扇与继电器是并联的,原来是按照12V设计。
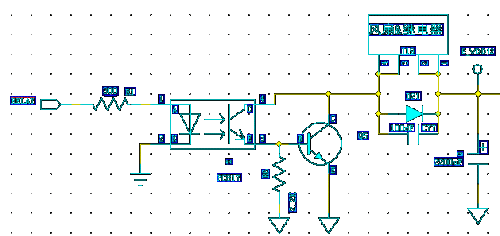
因为原设计认为,继电器和风扇的电流都不会很大,各自都有100mA附近,加起来也不过300mA,常规的光耦输出配三极管接法即可(这种电路自身有1V压降),因为三极管压降,实际到继电器及风扇中的电压为11V。在实际中也确实可以,但在生产了一批100多台后发现,个别机器,存在继电器不吸合现象,有些机器,甚至摆放颠倒一下,就会出现继电器不吸合,最后测试发现,这个继电器的开启电压太低,正常的都在9V附近,而个别的到了10V多,而因为三极管的这种接法导致1V压降,所以会引起一定的失效概率,于是为了安全起见,生产那边就把输出电压从12V提高到了18V,余量用的足足的,想彻底解决这个问题。
过了一段时间反馈发现,风扇内部的三极管会烧坏,并且国产的风扇,各个批次电流都不一样,生产那边也没辙,于是就让厂家不停的换风扇,最后导致这批接近1A的风扇出来这个事情。
了解清楚这个来龙去脉之后,让我感受到,生产人员的科学素养不足导致这类问题,本身这个问题很简单,但因为头疼医头脚疼医脚,最后没有了章法。
首先,继电器是工作在12V的,那就应该按照12V的标准来设计,对于继电器来说,只要测试发现电压高于9V的,就不能用,余量用3V即可。国产的一般质量无法控制,必然有一定的次品,把这个排除掉即可,而他们的测试方法往往不对,标称12V的,他们测试的时候,只知道用12V去测量,从来不去测下限。自从发现了下限这个问题,就盲目提高电压,导致继电器发热过高,接近4W,而这个又是继电器发热的上限,一段时间内估计没问题,但半年下来,继电器估计就要损坏。
对于风扇,因为可以在12~30V内都可以工作,考虑到12V风速太低,30V发热过高,取18V问题大不,但也要测试下限与上限,下限测它的启动能力,上限测它的发热及耐热特性,因为工作的坏境,温度很高,若在很高的电压下都能稳定工作,则热稳定性比较好。但是,风扇长期运行,过个2、3年一般都会坏,必须要考虑保险,尤其是它跟继电器线圈并联供电,必须要考虑好风扇短路后的问题。
基于这两点,还是采用18V下,在继电器上串联了一个60多欧姆的大功率电阻,让继电器还是工作在12V,风扇上,串联一个10欧姆的小功率电阻,正常情况下不影响风扇,一旦风扇短路,则电压都压降在这个10欧姆电阻上,让这个电阻烧坏断路而不影响继电器。同时改进三极管部分的压降,直接换成MOS管,再外部加有源驱动,实现MOS管零压降,这个问题才彻底解决。
在这个例子中,让各个器件都工作在他们的正常范围内,既要保证他稳定工作,又要保证不发热烧坏,还要考虑异常存在的处理。
通过这个例子,发现生产人员那边必须要抓基础培训,改善他们的科学素养,但这个面太广泛了,有点无处着力,但仔细分析基本上可以分为几类:
1、未做事之前,自己脑子里要有一个初步的答案,这样做完跟自己预估的比较,算是一个验算过程,实现闭环。
2、引入一个东西,有一利必有一弊,想到利的同时,要考虑到弊
3、测试,一定要深刻认识,知道各个参数的极限,而不是测量正常值。
4、看datasheet,完整的看完,不要只看几个自己认为重要的,出问题的,都往往是自己没有明白的参数。
5、不能光知道做实验,很多实验的结果往往是假的,蒙蔽自己的眼睛,因为它有时效性和具体性,做实验之前,必须要有理论分析。
6、坚持一看二想三做四检查流程。
7、学会推理分析,尤其是溯源,从源头解决问题,事半功倍
8、切勿养成依赖性,尤其是女生,往往出现技术依赖,而不能自主思考问题,继而影响创新能力。
有网友提到关于技术与生产的一些问题,我做一些回复:
1、高频感应加热项目(6000W、1MHz)是应东莞俊知机械有限公司要求设计配套产品,因其原来配套的供应商的高频机质量无法满足要求,不良率太高,并且他没有能力再进一步提高质量,而国外质量虽好但价格太高,国内找不到合适的情况下,我们被迫上的项目。
2、高频机技术是我在 2011年花了一年完成开发的,最后阶段2、3个月让一个刚毕业一年的具有一定生产经验而无研发经验和理论基础的大学生跟我开发学习。后续生产、细节改进由他和俊知公司一起改进,我因为还有别的项目要做,无法长期耗在这个项目中。也没有抽调华控的骨干来做,可以说是一个全新没有任何基础的团队开始的。
3、抽调了公司有一定工作经验(非研发、生产性质),做事态度认真的2个同事跟他一起跟俊知(客户)长期维护改进这个项目。所以这个团队相当于一个很弱的研发和生产队伍临时搭建的,加上生产要求很重,一年差不多就出了300多台,所以队伍一下子达到了8人,能外包的尽量外包了,这还不包括客户俊知负责的机械部分。
4、我一般偶尔去一下生产那边,解决实际问题,或者在QQ上完成指导设计修改。一些小的细节尽可能放手给他们做,而他们几个也确实足够努力,我没有要求,我也不在的情况下,他们一周六天制,住在公司,天天干活到夜里十一、二点。
5、他们的努力让我进一步放手给他们做,虽然问题很多,很多都是常识性的问题,不仅仅研发的,哪怕是生产的一些常识性的问题,他们都不停的犯,但他们积极热情的劲让我来承担产品质量出现问题的损失。因为我认为只有失败,才能让他们最快的成长,这不是在培养一个技术人员,一个生产人员,而是在培养一个企业家,一个老板。一个老板的培养,必须要大量资金下去给他玩。让他们自己痛苦,因为出问题的机器回来头痛的是他们自己,他们有切肤之痛,才能真正理解什么叫产品。只有这样,他们才能理解产品的每一个环节,而不是只是重视技术。实验证明,他们的发展速度非常快,因为他们从一个二三线完全不懂的大学生,只通过1、2年时间就变成了一个具备理解产品的老板思维。客户前期的不理解,抱怨到现在的肯定,让我们非常欣慰,并且这个项目运行中,始终没有干涉我自己的日常工作,轻松在家干活。
6、也就是因为出现了这么多问题,让我反思对这些低层次素质人员的培养该如何做,我们实力小,不具备请高薪高水平人员,但如何快速的把普通人员高速的提高层次满足要求,让他们实现价值,这是我长期所追求的,因为我要做的,也最想做的,是教育。