摘要:根据生产设计需要,采用AT89C52单片机对6PSD30-1型电子控制喷油泵试验台进行了技术改造,实现了主轴转速预置、测速和调速等多种功能,完成了燃油喷射系统喷油次数的预置、计数与计满后自动停止以及各种相关参数的显示,从而将传统的喷油泵试验台改造成为计算机控制的智能型喷油泵试验台,提高了试验台的可靠性,减小了维护和修理的工作量。
关键词:燃油喷射;喷油泵;试验台;AT89C52单片机;技术改造
0 引言
燃油喷射系统是柴油机的重要组成部分,其性能的好坏直接决定着柴油机的动力性、经济性和排放性。喷油泵是该系统中最重要的部件,喷油泵试验台是调整和测试喷油泵的主要设备。6PSD30-1型电子控制喷油泵试验台是20世纪70年代的产品,其电气控制部分电路采用大量分立元件构成,测试灵敏度低,设定调整不方便,故障率高,而且电路元件大多老化、损坏,现处于闲置状态。本文采用计算机控制技术,对其进行了技术改造。
1 智能型喷油泵试验台的技术改造方案
现有的6PSD30-1型电子控制喷油泵试验台,属于D系列电子控制无级调速型试验台,即可控硅转差离合器调速试验台。主电机功率为3 kW,主轴转速范围为120~1 200 r/min,量油计数基数次数100次,计数次数选择范围为100~500次;其动力部分和控制部分的电路采用分立元件,无试验油温监测和控制系统,量油部分采用传统的玻璃量筒目测,测试不方便且精度低。
目前,国外喷油泵试验台开始采用微机量油及数显系统。为此,按国际标准改进传统的结构以提高测试精度,达到以下要求:数字显示压力、温度、转速与计数(过去喷油泵试验台采用的机械式转速表、弹簧压力表和压力式指示温度计,很难达到国际标准要求);燃油恒温控制在40℃;自动控制倒油时间;数显油量与屏幕显示油量。
本方案以AT89C52单片机为整个控制系统的核心,采用模块化的设计方法对喷油泵实验台的喷油计数、主轴转数、油量显示及与上位机的通信进行控制,系统设计的结构总框图如图1所示。
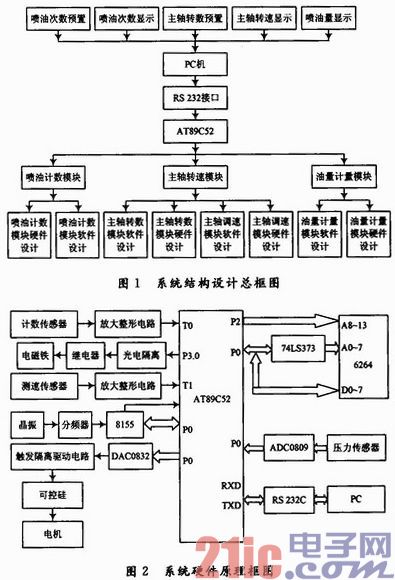
2 喷油泵试验台的硬件系统设计
喷油泵试验台的硬件系统设计分为喷油计数模块、主轴转速模块和油量计数模块三大模块设计,其中主轴转速模块又分为测速模块和调速模块。
系统硬件原理框图如图2所示。
考虑到对原有试验台进行技术改造,尽量采用较少的器件。系统硬件在AT89C52单片机最小化应用系统基础上外接设备:A/D转换器、D/A转换器、8155并行I/O芯片以及传感检测器、功率驱动电气接口、执行机构等构成一个控制系统。
从上位PC机键盘输入预置的喷油次数,通过上位机与单片机的通信传到单片机的数据存储器。按下集油按钮后,继电器吸合,通断油机构中与挡油板相连的电磁铁通电,挡油板拉出,实验油开始流入量筒,试验台处于量油状态。主轴转一圈,喷油泵喷一次油,AT89C52的T0利用计数传感器输出的脉冲进行计数。当喷油次数与预置值相等时继电器释放,使电磁铁断电,将挡油板推回,阻止喷油进入量筒,试验台处于断油状态。此时,量筒中的油量即是给定喷油次数的喷油总量。在量油的实时过程中,喷油次数从零开始显示,一直显示到预置的喷油次数。
速度给定由PC机键盘设定,AT89C52的T1计数和8155定时结合对从测速传感器来的脉冲进行计数、运算,测出实际转速。预置转速与实际转速之差经PID算法调节后输出给D/A转换器,然后通过触发驱动电路去改变可控硅的导通角,从而调节试验台电动机的励磁线圈电流,达到控制主轴转速的目的。PC机实时显示试验台电动机的转速。
3 喷油泵试验台系统的软件设计
软件设计采用Visural Basic 6.0和MCS-51汇编语言进行编程。本系统软件模块主要包括上位PC机模块、下位AT89C52单片机模块和通信模块。上位PC机模块主要是完成与操作人员的交互功能,包括参数设定、数据显示、打印、存储及监测;其中AT89C52单片机模块作为数据采集及控制模块,它包括系统初始化、喷油计数、测速、调速、采样、输入信号的处理、分析、并最后给出控制系统的输出量。
上位PC机模块的功能是完成系统与操作人员的交互,操作人员可进行参数设定、动态数据监测显示、查询标准调试数据、打印数据报表等。系统的动态数据显示设计方案如图3所示。

下位AT89C52单片机的主程序主要完成系统的初始化、与上位机握手、接收预置参数、调用主轴转速程序、调用喷油计数程序、调用数据采集发送程序。
图4为喷油泵试验台在不同转速、不同压力下的喷油量。
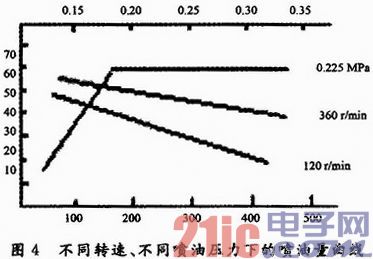
4 结论
本文所设计的系统已经成功地应用在北京型内燃机车和东风型内燃型机车柴油机喷油泵的测试平台上。
研究表明,本文提出的喷油泵试验台可以自动地控制喷油计数、主轴转速、试验油温和油压,实现了量油时压力、温度、转速、计数和喷油量的数字显示与屏幕显示,使用维修方便,提高了检测的精度和自动化程度。