摘要:介绍了填补国内空白的国产最大10 t真空自耗电弧炉用2x20 kA/60 V直流电源的系统构成。主电路采用12脉波双反星型可控整流,触发脉冲有相位自适应功能;高性能功率因数补偿控制器与8421编程的分组补偿容量配置,保证了投入补偿容量跟踪实际功率因数实时值变化,输出直流电流在10~40 kA的整个运行范围内功率因数都高于0.95;根据工艺状况起弧、熔化、补缩阶段的差异,变结构的电压与电流调节器状态根据负载工况自动切换,适应熔化重量不同锭子对输出电流大小的相异要求,稳流精度高达0.5%;矩阵式软件设计简化了PLC监控系统的硬件结构,取得了很好的控制与监控效果。
关键词:直流电源;真空电弧炉;电路设计
1 引言
直流真空熔炼是稀贵金属及高性能合金钢熔炼所必须采用的工艺,真空电弧炉及配套电源是其中的关键设备。我国熔炼钛的直流真空自耗熔炼炉,单炉熔炼重量已从原来常用的1 t提至10 t,这里介绍了用于国产10 t钛合金熔炼真空自耗炉的2×20 kA/60 V直流电源的设计及使用情况。
2 原理与设计
10t钛合金熔炼真空自耗炉工艺要求配套直流电源输出额定参数为40 kA/60 V,其构成可分为主电路及控制电路两部分。
2.1 主电路
主电路采用10 kV经两级变压器直接降压再由晶闸管可控整流的方案,为降低注入电网的谐波含量,采用12相可控整流方案,考虑到熔炼过程中起弧电压为60 V,而熔炼电压仅为40 V左右,功率因数很低的实际工况,主电路中增加了功率因数补偿环节。图1示出主电路原理,其中应用了两套双反星形可控整流单元并联。
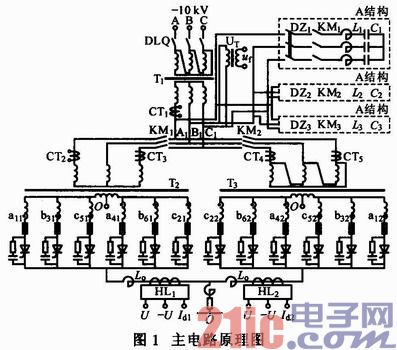
(1)降压匹配变压器 电网10kV先由第一级变压器降为690 V,再由两台初级分别接为三角形与星形的整流变压器降压,这样设计是为了将第二级整流变压器与可控整流部分装在一个柜体中,构成一体化电源,从根本上解决多年来,该类国产电源整流变压器放于柜外,现场安装整流变压器与整流柜之间大截面铜母排极难安装,工作量巨大的问题,此结构方案吸收了世界先进技术设计,变压器T1采用油浸自冷,而整流变压器T2与T3采用干式水冷,CT1~CT5为进行690 V侧交流电流取样的电流互感器,其作用:①在直流霍尔电流传感器失效后,为原电流闭环系统变为开环运行故障的过电流保护提供电流取样信号;②为功率因数控制器提供计算功率因数的电流取样信号,电压互感器UT用来把690 V电压变为功率因数控制器需要的100 V标准信号,作为功率因数控制器计算功率因数的电压依据。
(2)可控整流部分 该部分的电路原理构成如图1中的下半部分,采用两个双反星形可控整流电路并联,HL1与HL2为霍尔电流传感器,用于检测每个整流部分输出的实际电流值,提供给闭环调节器及保护单元与显示环节,保证在同一个输出电流设定值下,两个双反星形可控整流部分各承担负载电流的一半,另外在对实际运行电流进行实时显示的同时,提供给保护电路监控运行状况,若超过实际值,则进行有效迅速的保护。
(3)功率因数补偿的主电路 几乎所有的真空熔炼炉都是空载起弧电压高,随单炉可熔炼金属材料重量的不同为50~75 V,熔炼过程中熔化电压一般为30~45 V,因此运行时其功率因数都很低,一般为0.45~0.7。为解决此40 kA直流电源系统功率因数太低的问题,首次在此领域使用的可控整流电源系统中,增加了按熔炼过程中实际负荷功率大小自动调节功率因数的环节,其主电路如图1右上角所示,图中DZ1~DZ3为进行电容短路故障保护的自动空气断路器,KM1~KM3为用来按实际功率因数大小自动投切补偿支路的接触器,L1~L3,C1~C3分别为3个支路中防止谐波放大的电抗器和功率因数补偿电容器,该功率因数补偿主电路的工作原理为:装设于控制回路的功率因数控制器,根据UT与CT1的电压和电流取样信号,实时计算功率因数,根据计算结果与目标值0.97的差别,以8421编码的组合方式,输出控制KM1~KM3中1个、2个、3个闭合,按功率因数的实际需要投入相应的补偿电容,满足无论是化一次锭还是化二次锭,在输出直流电流从10~40 kA变化的整个工作范围内,都可以保证690 V侧的功率因数既不低于0.97又不高于1。
2.2 可控整流部分的控制电路
可控整流部分的控制电路分为给定积分、闭环调节器、电压电流检测与处理、同步环节、触发脉冲形成和保护监控电路,限于篇幅在此仅介绍几个关键的单元电路。
(1)闭环调节器 由于真空电弧自耗炉工作有起弧、熔炼、补缩等工艺过程,空载起弧与熔炼工作时电弧电压相差一半,熔炼过程中又希望构成稳定度很好的恒流源,为防止起弧时电压太低无法起弧或起弧电压太高击穿坩埚,设计了图2所示的动态双闭环调节器,其起弧时为稳压源,熔炼时为恒流控制,并可按负载工况自动转换。
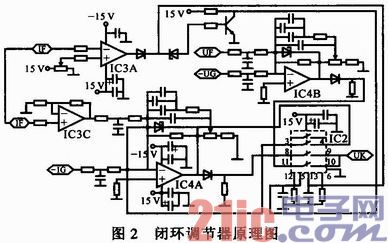
图中IC4B与IC4A分别和外围元器件一起构成PI调节器。UF与IF分别为来自电压与电流检测环节的输出信号,电压与电流的检测均使用了
霍尔传感器,IC2为电子开关CD4066,在起弧前因IF几乎为零,比较器IC3A输出高电平,IC2中引脚6为低电平,引脚12与5为高电平,其内部引脚11与10接通,反馈为电压反馈,电压闭环调节器工作,构成电压闭环;引脚3与4相接,对电流调节器锁零。当起弧成功后,由于电流值通常已达几千安培,IC3A输出低电平,IC2中的引脚12变为低电平,电压调节器输出支路因IC2的引脚11与10断开而退出运行,同时IC2的引脚6变为高电平,电流调节器输出支路因IC2的引脚8与9接通而投入运行,电流取样值作为调节器的反馈信号送入电流闭环调节器,从而保证直流电源输出为稳定度很好的恒流源,满足熔炼过程中高精度稳定直流电流输出的需要。
(2)同步环节 10t钛合金熔炼真空自耗炉用2x20 kA/60 V直流电源,应用了光耦合器作为触发脉冲形成单元前级的同步环节,使同步环节的体积及损耗都得以减小,而且为构成相序自适应的触发器奠定了很好的基础,图3中6个光耦合器均为TLP521,由此决定了同步环节的输出为6路相位互差60°的方波脉冲信号。
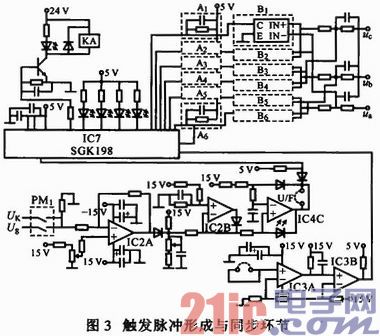
(3)触发脉冲形成 触发脉冲形成环节的原理电路如图3所示,其核心单元IC7为应用CPLD芯片开发的准数字化触发集成电路芯片SGK198,该触发器将闭环调节器输出的电压信号变换为与此电压相适应的频率脉冲信号,在SGK198内对这一脉冲信号进行6分频计数的方法来获得6路触发脉冲输出,6路触发脉冲形成的计数器开始计数的时刻由同步环节输出的6路同步信号的后沿所决定,当差分器IC2A输出电压低时,压控振荡器IC4C输出的频率便低,计数器计满的时间便长,输出触发脉冲距同步信号后沿距离便远,IC2A输出电压便高,IC4C输出频率便高,计数器计满的时间便短,输出触发脉冲的时刻距同步信号后沿距离便近,相当于控制角α增大,晶闸管的导通角减小,输出直流电压降低。
(4)监控保护单元 10t钛合金熔炼真空自耗炉用2x20 kA/60 V直流电源,应用PLC完成运行状况的监控及故障时的保护工作,图4给出了监控与保护环节的软件流程框图。由于两台整流电源共用了48只晶闸管元件,报警信号很多,为减小PLC系统的硬件配置,电源系统采用了一种矩阵式编程方法,从而使系统硬件得以简化,同时在软件编程时根据电弧熔炼的特殊要求,增加了给定不为零不能合闸起动环节,主电路合分闸都在脉冲封锁状态下进行,功率因数补偿环节在电源输出功率达到一定值时才投入,在切除电源功率前先切除功率因数补偿单元,从而有效地防止了次谐波振荡及过补偿状况的发生。
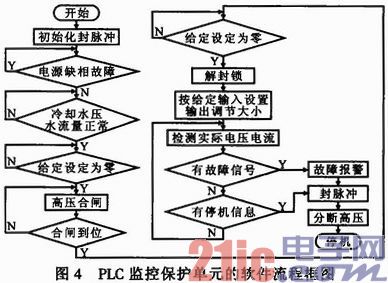
(5)熔速控制及自动给定 通过与炉子工况及熔炼控制的上位计算机之间的通讯,实现了自动熔炼时的按曲线给定,控制单元通过PLC接口接收上位计算机输出的按工艺设定输出电流指令,在PLC内转换为相应的模拟给定电压后从PLC的模拟输出口输出,控制触发脉冲的控制角相位,达到调节及稳定输出电流的目的,并在国内首次使用了熔速控制,满足全自动熔炼的需要,使控制达到了很好的效果。
(6)应用电流断续补偿扩大电流稳定不断弧范围 由于真空自耗炉工艺有起弧、熔炼、补缩等工艺过程,为保证成品锭快熔化完时使锭子端口尽可能的平整,提高熔化锭子成品率,要求补缩电流尽可能小。尽管在主电路中直流输出端增加了平波电抗器Lo,但也很难使输出直流电流达到全范围连续,因而在控制回路中增加了电流断续的补偿环节,使补缩时的电流连续稳定工作范围达到了最小电流不大于500 A的良好效果。
(7)功率因数补偿环节的控制 由于真空自耗熔炼炉工艺过程较为复杂,对应不同的工作段,要求输出稳定运行的电流与电压值不同,由此造成电源运行时其功率因数会有很大不同,这就决定了对其功率因数补偿环节要采取变化的参数与结构。在该系统中,根据系统最小短路容量计算的注入电网谐波满足国标要求,仅考虑功率因数补偿,这就决定了其控制电路既要满足起弧、熔炼、补缩、停机等工艺流程的需要,又要适合熔炼一次锭、二次锭、合金锭及锭子直径不同对直流电源输出电流的要求不同的需要,为此设计了专门的控制器,电源运行的实时功率因数按输入的电压和电流值随时进行计算,并按熔炼工况及所熔化锭子种类和实际使用电流的不同,按8421组合决定投入多大的补偿容量,既严格保证在整个工作周期中补偿后的功率因数大于0.97,且使谐波不被放大,又可靠地按当电源负荷达到一定值时,功率因数补偿支路才投入,而当电源负荷小到一定值时,功率因数补偿支路先切除,在直流电源停机时,先退出功率因数补偿支路,再断开图1中的断路器DLQ,保证不发生次谐波振荡及使谐波放大等不正常情况。
3 实用效果简介
上述10 t钛合金熔炼真空自耗炉用2x20 kA/60V直流电源,已成功在国内首台10t电弧炉熔炼系统中使用,随坩埚尺寸的不同,单炉可熔化锭子重量为6 t,8 t,10 t,最大锭子直径为1 020mm,整流变压器、直流平波电抗器、晶闸管整流单元、控制环节、纯水冷却器、进线断路器全部装于两个柜体中,每个整流柜系统输出20 kA/60 V,使用中两柜并联运行,经实测稳流精度高于0.5%,功率因数不论是在熔化一次锭还是二次锭,电源输出电流稳定运行范围10~40 kA,全范围内都不低于0.95,注入电网的谐波电流含量低于国标允许值,补缩工况最小可连续稳定运行电流为500 A,现场安装仅需连接交流三相输入690 V电缆线及直流输出正负母排和外循环水两根水管,安装甚为方便,运行稳定可靠,达到了十分理想的设计与运行效果,图5给出了熔化时输出的直流电压波形。
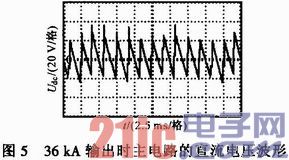
4 结论
10t钛合金熔炼真空自耗炉用2x20 kA/60 V直流电源,将整流变压器、平波电抗器、纯水冷却器、整流及控制和保护等单元装于一个柜体中,缩短了引线尺寸,减少了占地面积及现场安装工作量,是个很好的方案;介绍的同步环节及触发脉冲形成电路设计较为巧妙,可推广到低压可控整流系统;电压与电流可根据工况自动切换的闭环调节器设计,兼顾了稳定输出电压与输出电流的不同需要;采用12脉波可控整流,同时增加动态功率因数补偿环节,通过巧妙的控制器设计,满足了真空自耗炉的复杂运行工况要求,使运行时的功率因数较高,并保证了注入电网的谐波不被放大,在该行业为首创,在国内真空自耗熔炼炉及凝壳炉电源的系统配置中具有推广性;介绍的PLC监控与保护单元应用矩阵式软件编程方法,使需要的硬件配置要求得以降低,节约了成本,具有创新性;理论分析和实用效果都证明了上述方案的可行性,其应用前景将十分广阔。