激光惯性约束核聚变是中国工程物理研究院承担的国家级科学研究项目,其目标是利用强激光轰击氘氚靶丸,产生受控惯性约束核聚变而释放出聚变能。其中原型装置靶场光电控制系统是保证多路激光束精确引导、投射、基频倍频、精确聚焦的重要组成部分。它首先需要根据靶场反射光路的实际情况自动调整投射和引导反射镜的姿态完成激光的准直引导,然后控制三倍频晶体的匹配角使打靶激光能够按最佳角度入射到KDP晶体中,最后精确修正聚焦透镜的离焦量将激光的焦斑调整到坐标系的基准点。系统要求的设计精度非常高,由靶场瞄准定位控制系统所引入的误差不超过10μm,并且运动机构多且分散,对控制及监控系统在设计理论和技术方案实施方面都提出了很高的要求。适应这种控制要求的系统,一般称之为集散控制系统(DCS,Dist曲utedControlSystem)。PLC以其特有的高可靠性和不断增强的功能,使它在集散中发挥着越来越重要的作用,并且有取代专用Dcs控制器的趋势。
1 控制系统的功能和结构
根据物理实验的要求,原型装置的靶场系统需要将12束激光从真空靶室的上方和下方以一定的角度射入真空靶室并经三倍频器、聚焦透镜精确引导至靶点(激光在靶场将依次经过大口径高精度反射镜架模块、终端光学组件模块)。以此为基础,针对核聚变的前沿性物理问题展开探索性实验研究。
光学组件运动控制系统包括反射镜架模块与终端光学组件模块两大部分,共同调节12束激光准直至物理实验靶的指定位置。图1给出了控制系统的结构框图。运动控制系统的设计功能是,“本地控制”工控机(IPC)根据“远程集中控制”系统的指令完成各个光路的准直调节,状态监控,参数和重要数据记录等工作,从而为激光发射做准备。
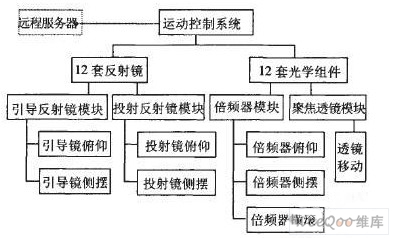
图1 系统结构框图
由于控制电机数量较多(48台伺服电机和48台真空步进电机),而且空间位置分散,因此光学组件控制及监测系统采用了分布式控制技术,通过工业控制网络组成先进的过程控制系统和实时、可靠的监控系统。由上位监控计算机对系统进行全面的监控和管理;由安装在现场的48台日本松下公司型号为FP-e的PLC控制器作为下位控制器与现场电气设备和执行机构直接连接,执行可靠、有效、具体的分散控制。系统的上位IPC与现场的各PLC控制器距离通常较远,为保证系统的可靠性,采用RS485标准总线网络进行数据传输,这样就构成了分布式控制网络。由于采用了网络拓扑结构,系统扩充非常方便灵活,可适用不同规模系统的控制要求。
系统的控制器和执行机构较多,因此,在设计控制箱时采用了模块化的设计思想。每路激光的控制由8个运动轴单元构成:引导反射镜俯仰轴和侧摆轴,投射反射镜俯仰轴和侧摆轴,倍频器俯仰轴、侧摆轴和滚动轴,以及透镜移动轴。每路激光的电机控制集中在两个控制箱中,分别称作反射镜架控制箱与终端光学组件控制箱,作为分布式控制网络的终端。每一个运动轴的控制由PLC、驱动器、电机、通讯适配器等组成.各控制箱与工控机之间同RS485总线进行信息传递系统的硬件配置如图2所示。工控机将位置指令发送给PLC,经驱动器功率放大后由电机带动精密丝杠螺母副驱动反射镜及终端光学组件运动。各运动坐标的极限位置由接近开关检测,以开关量信号形式输入PLC进行处理.各光路反射镜、倍频器和透镜的调整电机可同时工作。
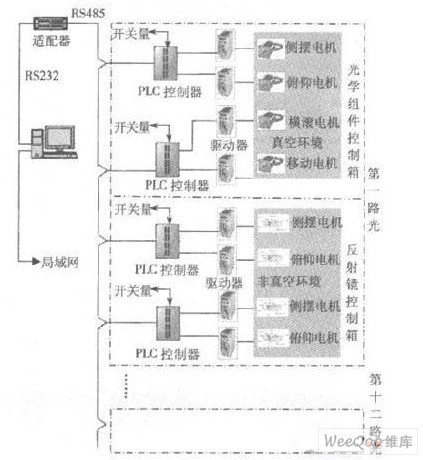
图2 控制系统硬件配置示意图
2 系统通讯
系统采用RS485标准总线,具有速度快(最大位速率为10 Mbps),传送距离远(90 kbps速率下可传输1200 m)的特点。RS485以差分平衡方式传输信号,具有很强的抗共模干扰的能力,允许一对双绞线上一个发送器驱动多个负载设备。各节点下位PLC均带有RS485通信接口,在本系统中上位IPC通过RS232/RS485接口转换器提供上位机网络节点。在总线末端接一个匹配电阻,吸收总线上的反射信号,保证正常传输信号干净、无毛刺。
在1∶N通信方式下,每台PLC被分配不同的地址,上位机与PLG采用统一的通信协议,上位机优先发出呼叫并启动通信。上位机通过RS485网络广播自己所要求的下位PLC地址,所有PLC都收听广播,记下广播地址。各PLC把收到的地址与自己的地址进行比较,地址相同的PLC为被选中的下位机,其余PLC皆为未选中的下位机,暂时从网络上隔离。网络上只剩下主机与选中的PLC,按主从式的通信过程进行通信。上位机采集PLC数据后根据新收到的数据刷新监控画面。
上位IPC与下位PLC既相互通信构成一个完整的信息采集系统,又能彼此独立工作,一旦上位IPC出现故障,下位PLC可脱离上位机独立工作,确保现场设备安全、可靠连续的运行。
本系统所用控制变量较多,共需1500多个,因此,IPC与各PLC之间的通讯采用了北京亚控公司的组态软件组态王6.5开发。组态王把每一台下位控制器看作是外部设备,在开发过程中按照一定要求完成设备配置过程。在运行期间,组态王通过驱动程序和这些外部设备交换数据,包括采集数据和发送数据/指令。每一个驱动程序都是一个COM对象,这种方式使通讯程序和组态王构成一个完整的系统,既保证了运行系统的高效率,又使系统能够达到很大的规模。组态王通过串行口与PLC进行通信,访问PLC相关的寄存器地址,以获得PLC所控制设备的状态或修改相关寄存器的值。在实际编程过程不需要编写读写PLC寄存器的程序,组态王提供了一种数据定义方法,在定义了L/O变量后,可直接使用变量名用于系统控制、操作显示、数据记录和报警提示。
3 系统软件开发
3.1 远程服务器通讯模块开发
本地控制工控机与远程服务器端采用基于TCP/IP协议的Socket技术进行通信,由VC++6.0编程工具开发。本地控制计算机在5002端口侦听远程服务器发来的数据包,远程服务器在5003端口侦听本地控制工控机发去的数据包。通讯模块的主要功能有两个:接受总控服务器发送来的数据包并进行解析;对要发送的信息构造数据包并发送,IPC与远程服务器之间的通讯数据为二进制格式,长度不固定。数据包由发送者识别号、接收者识别号、功能代码、参数长度、参数内容等5个部分共(16+N)个字节组成。OPC(OLE for Process Control)在当今的过程控制领域是一种非常流行的数据交互技术。下位控制器与系统通讯模块的连接通过0PC接口实现。VC编程调用组态王提供的OPC动态链接库接口函数,实现了下位控制器与远程服务器的通讯。
3.2 PLC系统控制模块开发
下位控制器采用状态设计法编制程序梯形图。系统的运行和故障联锁全部由PLC控制,以提高系统的可靠性;在软件设计中添加了各种联锁条件,使各动作间能够严格确保相互约束或定时关系;通过建立适合的状态标志位,实现了识别及处理故障的能力。控制程序从功能上可分成4个模块:1)开机画面设置及初始化模块;2)手动模块;3)报警、限位处理模块;4)自动模块。
3.3 上位机监控软件设计
组态软件KingView6.5由工程浏览器TouchMAK和画面运行系统TouchVew两部分组成,具有强大的图形编辑功能。运用开发环境TouchMAK设计监控软件,监控软件实现的系统功能包括:显示工艺流程图和各种参数实时测量值;实时修改下位机所需的各种参数的数值;上位机和下位机之间的通讯管理;实时显示故障报警画面;实时数据库和历史数据库管理;生成系统日志报表;将过程监控站中的各类实时数据、画面、图表等信息存入本地的网络服务器中。采用Access数据库保存历史记录,数据库中当天的操作记录在一个数据表中,数据表以用户名、年、月、日命名。TouchVEW是显示TouchMAK中建立的图形界面的运行环境。上位机监控系统运行时运行TouchVEW进入监控主画面,各设备的状态就以动画的形式形象的表示出来,通过主菜单或各画面的功能键,操作人员可方便地切换各画面,获得各画面具体的监控数据。
4 结 语
本文研究的基于PLC和组态软件的光学组件自动控制系统,利用了PLC可靠性高、抗干扰能力强的特点,又利用了组态软件强大的数据处理和图形表现能力,融合了较先进的自动化技术、计算机技术、通讯技术,具有可靠性高、操作简单、维护容易等特点。该方案已成功应用于激光惯性约束核聚变靶场光路系统的设备监控,取得了满意的效果,其控制原理对其他分布式控制系统具有一定的借鉴作用。
参考文献:
[1].PLCdatasheethttp://www.dzsc.com/datasheet/PLC_1248813.html.
[2].RS485datasheethttp://www.dzsc.com/datasheet/RS485_585289.html.
[3].RS232datasheethttp://www.dzsc.com/datasheet/RS232_585128.html.
[4].COMdatasheethttp://www.dzsc.com/datasheet/COM_1118194.html.